CHM SERIES
Charging, stoking and distribution machines
On a furnace platform space is usually very limited. The special design of the lever system makes our CHM Series machines extremely compact and space-saving.
Thanks to the high-speed movements and the excellent maneuverability of these machines, door opening times at the furnaces can be kept extremely short.
HIGHLIGHTS
The parallel-lifting design of the lever system enables extensive vertical movements despite its very compact dimensions.
The telescopic jib of the machines ensures a long reach when stoking or distributing materials in a furnace. For ease of maneuvering, the jib can be retracted when not in use.
The machines of the CHM series are designed to operate in high-temperature environments. All components are safely protected to withstand even the most intense heat sources.
Activities such as charging, deep-stoking, cracking of baked slag and even piercing of gas bubbles can be performed with just one machine. The operator can change the tools quickly and easily without having to leave the cabin.
Automatic safety circuits ensure protection of the operator and the machine in case of an accidental contact with an electrode.
The benefits at a glance
- Very compact design
- Excellent maneuverability
- Tool change without manual intervention
- Maximum safety
MORE DETAILS
Mobile
Thanks to their very compact design, the machines of the CHM Series have proven their worth, especially in the confined spaces typical of furnace shops. The central rear wheel gives the machine the highest maneuverability, enabling the CHMs to turn virtually in place.
When stoking or distributing material in the furnace, the telescopic jib can be extended, giving it an exceptionally long reach.
Rail-bound or craneway-mounted
In addition to our mobile machines, we supply program-controlled machines that can serve one or several furnaces. These machines move on rails or are suspended from a craneway.
The machines further optimize the reduction process, since all charging, stoking and distributing tasks are program-controlled according to a predefined sequence and are in exact compliance with the metallurgical specifications.
In addition, they help reduce the energy consumption of the furnace, boost the furnace’s capacity and prevent damage to the refractory material or the electrodes.
Maximum flexibility of motion
The parallel-lifting lever system provides maximal flexibility of motion in both the vertical and horizontal directions.
High flexibility
The skip charges specified quantities of material into the furnace and is emptied by turning the jib or by means of a telescopic sliding device. The stoking tool is used for stoking deep into the metal charge in the furnace, to crack baked scrap and to pierce gas bubbles. For furnaces equipped with a charging pipe, this tool can also be used to distribute the charged material inside the furnace.
Forks are used, for example, to feed copper rings into the furnace in a controlled manner.
The operator can change all these tools without leaving the cabin.
Tailored energy supply
Most of the CMS machines operate near furnaces. Due to the very high temperatures to which the machines are exposed in this operating environment, we usually supply the machines with an electrohydraulic drive. The power supply is either via a festoon cable or a contact line.
Machines serving several furnaces in different shops and having to cover longer distances are usually equipped with diesel-hydraulic drives.
High-precision control
The proportional valves of the hydraulic system enable a high precision and highly sensitive control of the machine and the jib in particular.
The driver’s cabin of our mobile machines is arranged off-center. This provides the operator an unobstructed view into the furnace and around the machine.
High availability
The sturdy design, the central hydraulic block and the use of hydraulic hoses instead of pipes make the CHM extremely maintenance friendly.
The optional D&D Connect system sends the machine data to a server where the user can evaluate the available data in a central source. Therefore, it is possible to always stay informed on the current state of the machine and to schedule the maintenance activities more efficiently.
This knowledge is especially helpful to users who operate multiple CHM machines, thereby allowing them to schedule the maintenance team’s assignments to maximize the availability of the complete fleet.
Safe working near the furnace
All machines are equipped with a hermetically encapsulated hydraulic system to provide the highest safety even given the extremely high temperatures at and near the furnace.
The mobile machines are equipped with a closed driver’s cabin that protects the operator from heat, dust and noise. The cabin can additionally be fitted with an air conditioning system, as an option.
As the mobile machines move freely about the furnace bays, effective safety precautions are essential. Therefore, the machines can be equipped with an optional laser scanner to watch the area behind and to the sides of the machine.
When the machine is reversing a blue spot projected onto the floor warns persons not to approach the vehicle.
In the event of a power supply failure an emergency generator will take over. This guarantees that the machine can be moved out of the danger zone safely.
Automatic safety circuits ensure that the operator and the machine are well protected in the event of an accidental contact with an electrode.
The mere fact that no operator has to be present on the furnace platform makes our rail-bound machines very safe. In addition, safety circuits integrated into the program control ensure that the refractory lining of the furnace and the electrodes will not be damaged by the machine.
For maintenance activities the machines travel from the operating area to a protected parking and service position.
Technical data
Max. payload of charging skip for ferro-alloys
kN
Max. payload of charging skip for steel and NF-metals scrap
kN
Max. extendable length of telescopic jib
m
Contacts
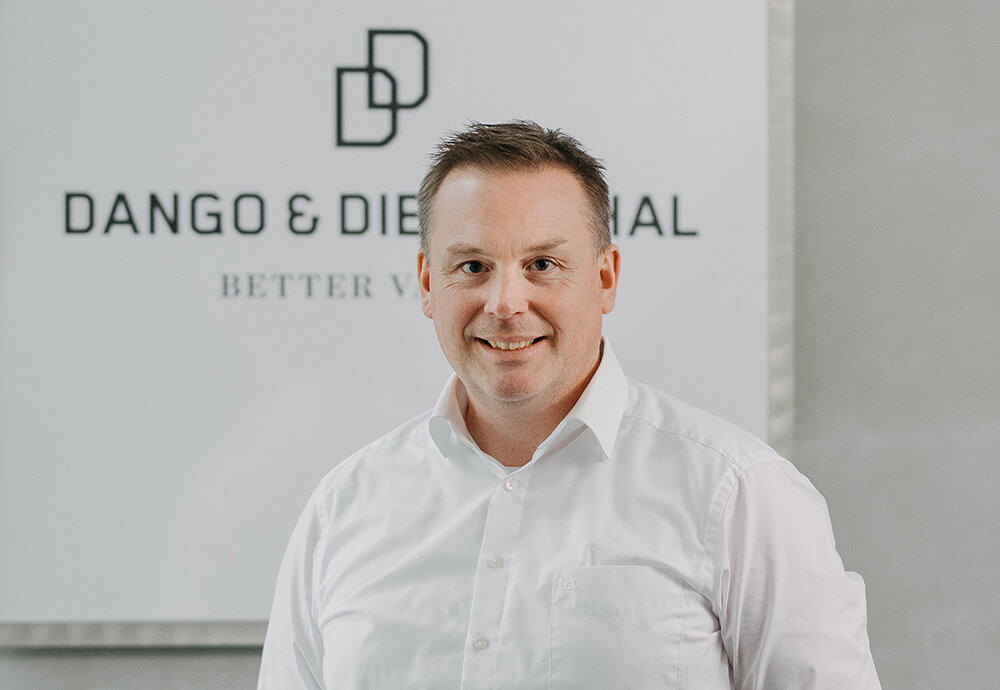
Herr
Andree Nöh
Senior Sales Manager
T +49 271 401-4491
andree.noeh@dango-dienenthal.de
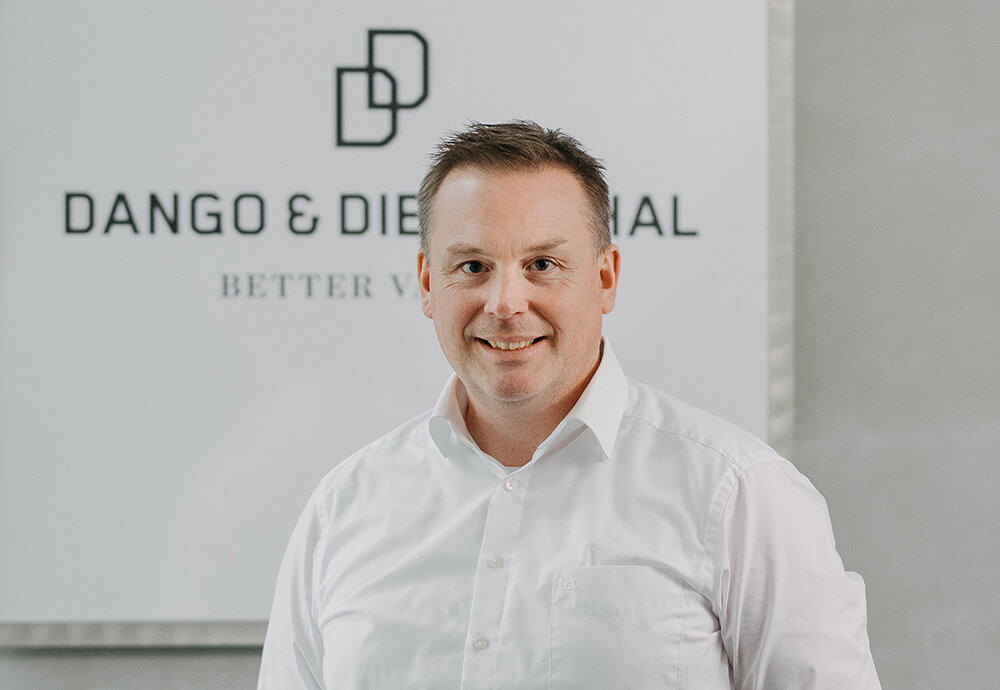
Herr
Andree Nöh
Senior Sales Manager
T +49 271 401-4491
andree.noeh@dango-dienenthal.de
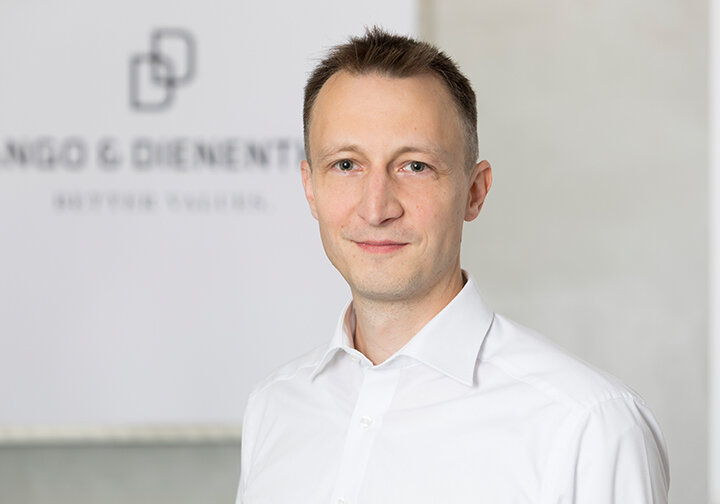
Herr
Boris Marcukaitis
Senior Sales Manager
T +49 271 401-4120
boris.marcukaitis@dango-dienenthal.de
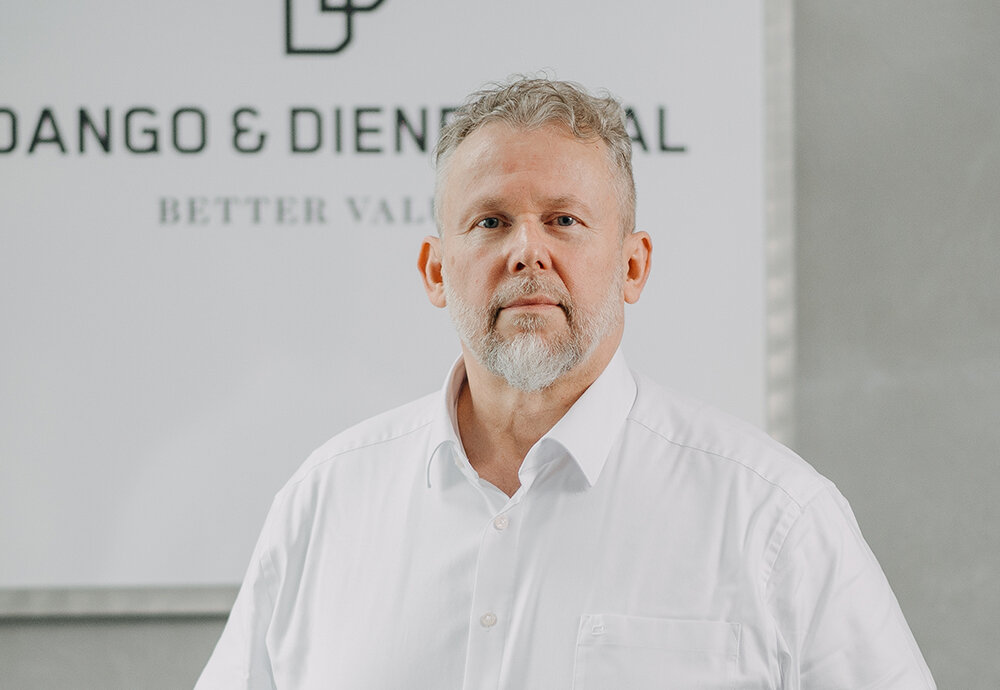
Herr
Volker Witzleb
Senior Sales Manager
T +49 271 401-4433
volker.witzleb@dango-dienenthal.de
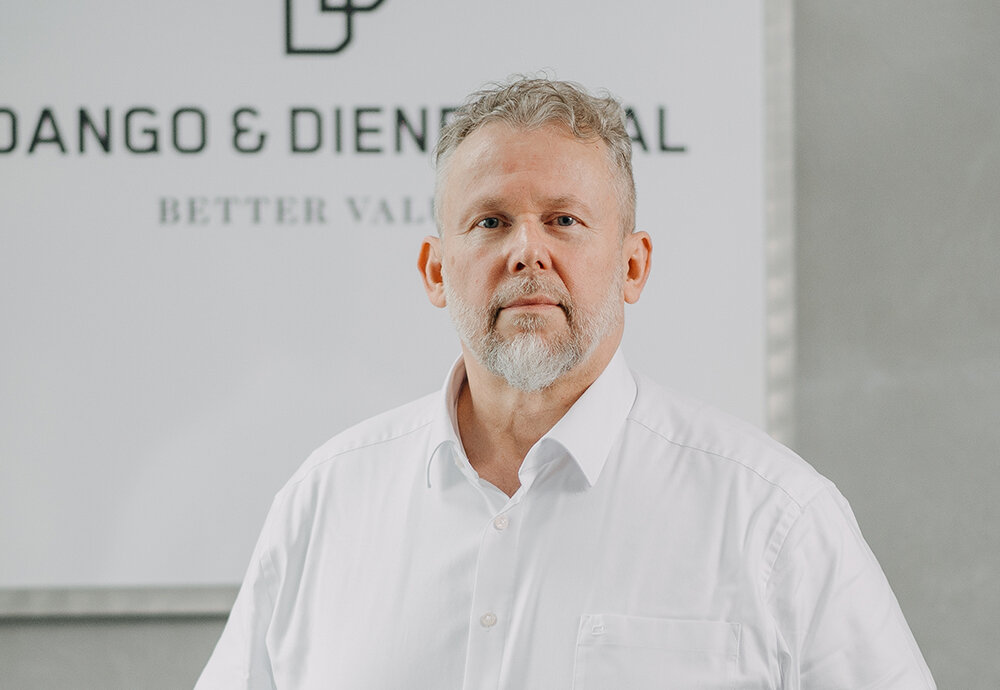
Herr
Volker Witzleb
Senior Sales Manager
T +49 271 401-4433
volker.witzleb@dango-dienenthal.de

Iysa Demir
Sales Manager Service
T +49 271 401-4332
iysa.demir@dango-dienenthal.de