MTM SERIES
Mobile transport manipulators
Our free-driving transport manipulators are designed for the transfer of ingots, slabs, ring blanks and rings within the forging shop area, for example to load and unload the furnaces and transfer the forgings quickly and safely between the furnaces and the presses.
Our mobile transport manipulators are faster than cranes and more efficient than forklift trucks. And they are specifically designed to cope with the demanding operating environments in forging shops.
HIGHLIGHTS
The mobile transport manipulators built by DANGO & DIENENTHAL are notable for their extraordinarily long reach combined with an unparalleled load-carrying capacity. Ideal in cases where the forging has to be placed at the far end of the furnace. The compact design of the manipulators makes them easy to maneuver. This and their high speed significantly reduce transfer times in the forging shop.
The manipulators of the MTM are designed to operate in high-temperature environments. Their exceptionally long jibs assure that all key components are at a safe distance from heat sources.
THE BENEFITS AT A GLANCE
- Long reach
- Very compact design
- Designed to cope with high temperatures
- High working safety
More Details
Made for the challenges in a forging shop
Thanks to its compact design the MTM is the manipulator of choice for confined spaces as frequently found in forging shops. The central rear wheel gives the machine highest maneuverability enabling the MTM to virtually turn on the spot.
We are familiar with the challenging operating environment in forging shops. Therefore, we know how to protect our machines safely against extreme heat. The unparalleled jib length assures that all key components stay at a safe distance from the furnace.
We supply the machines of the our MTM series with customized lever systems for specific applications:
- The parallelogram-type tongs can reach up to 3.5 or more meters high.
- The articulated system is the perfect choice for areas of limited space. By actuating an additional extension, the reach can be increased by up to another 2 meters without having to move the manipulator.
- The lifting mast lifts the tongs upwards – in a precise vertical movement, no matter what the operating conditions – to place a forging in a die, for example. In addition, this design is best suited for applications that require reaching very great heights.
Conditions and requirements are different in every forging shop. Therefore, we customize our machines to the specifics of the task on hand using our proven modular system.
Adapted to local operating conditions
We supply our MTM manipulators powered with diesel, gas or an electrohydraulic drive or with our new battery-based electric drive.
Most of our customers choose the electric drive variant with connection to the power supply system. For ease of cable handling the system comes with a counterweight cable reel.
Diesel and gas powered machines are predominantly used for applications that involve the coverage of longer distances.
A tight grip on all workpieces
The customer can choose from a great variety of lever systems and tongs designs to get the best solution for his application. For example:
- Eccentric tongs for loading and unloading ingots into chamber furnaces are designed to reach far into the furnace.
- Tongs for ring blanks and rings come with a rotary drive. Rings are gripped at both their inside and outside circumference. Deformation is securely avoided as the holding pressures are adjusted to the characteristics of each individual workpiece.
- Frontal gripper tongs are used to transport ingots in transverse orientation.
- We supply customized tongs designs for specific applications. With the optional quick-change device the tongs can be exchanged in a matter of minutes.
Safe transport guaranteed
The MTM manipulators are operated manually. The driver’s cabin is typically positioned off-center ensuring that the driver has a good view of the workpiece, even when this is positioned at the far end of the chamber furnace. At the same time, the off-center position of the cabin provides the driver a clear view of his surroundings.
Highly sensitive steering and actuation of the machine and the tongs are ensured thanks to the use of advanced proportional valve technology.
With the optional remote control feature the machines can be operated from a safe distance or even from the control room.
“Autonomous driving” is currently one of our key areas of development, as we see here great potential for speeding up processes, increasing operating flexibility and improving safety at the same time.
High availability thanks to low maintenance
The sturdy design, the central hydraulic block and the use of hydraulic hoses instead of pipes make the MTM extremely maintenance-friendly.
The optional D&D Connect system sends the machine data to a server where the user can evaluate the available data in a central place. Therefore, he or she always stays up to date on the current state of the machine and can optimally schedule the maintenance activities.
Especially where a user operates several MTM manipulators, this knowledge is helpful to schedule the maintenance team’s assignments with a view to maximizing the availability of the complete fleet.
Camera and scanning systems maximize safety
The operator cabin – fitted with a protective enclosure and safety glass – provides maximum protection, while being ergonomical. If requested the cabin can additionally be fitted with an air conditioning system.
As our mobile transport manipulators will be used to move freely about the forging shop, effective safety precautions are essential. For maximum safety at work the machines can be optionally fitted with a laser scanner, which watches the areas next to and behind the machine.
As a further option, a 270° bird view camera can be installed to watch these areas, giving the operator even more confidence when maneuvering in confined areas.
Low energy requirements
The integrated load sensing system ensures energy-saving operation, as it adjusts the power generated by the hydraulic system exactly to the current demand.
Technical data
Carrying capacity
kN
Range of tongs
mm
Block tongs gripping range
mm
Disk tongs gripping range
mm
Upper stroke position of tongs
mm
Drive power
kW
Contacts
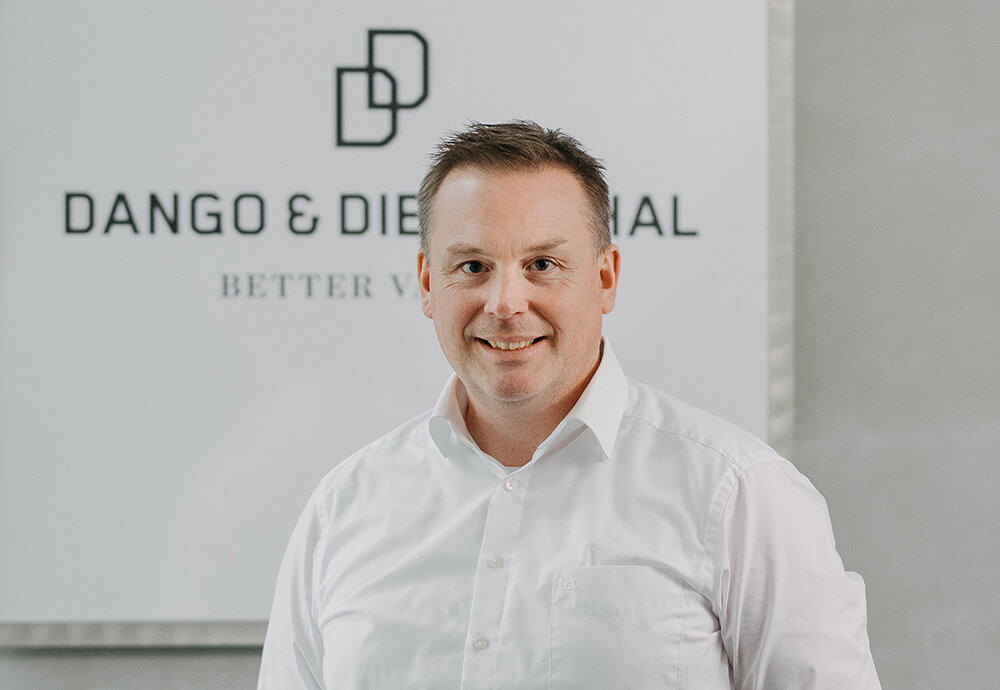
Herr
Andree Nöh
Senior Sales Manager
T +49 271 401-4491
andree.noeh@dango-dienenthal.de
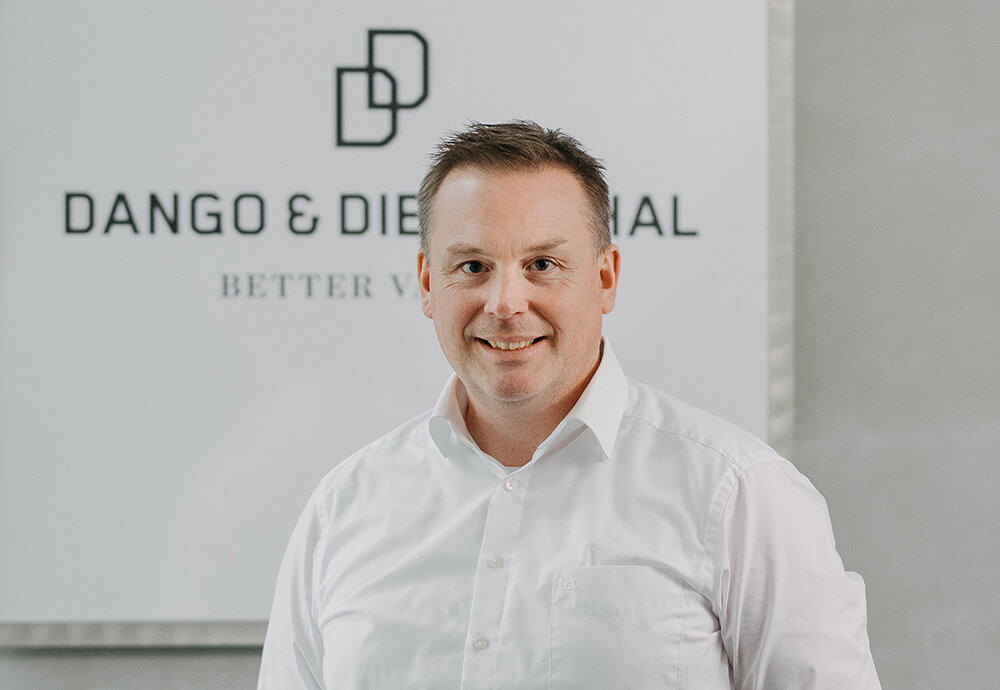
Herr
Andree Nöh
Senior Sales Manager
T +49 271 401-4491
andree.noeh@dango-dienenthal.de
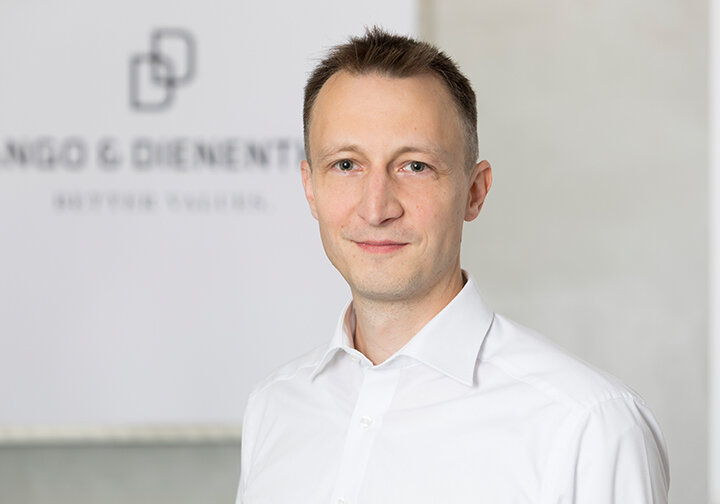
Herr
Boris Marcukaitis
Senior Sales Manager
T +49 271 401-4120
boris.marcukaitis@dango-dienenthal.de
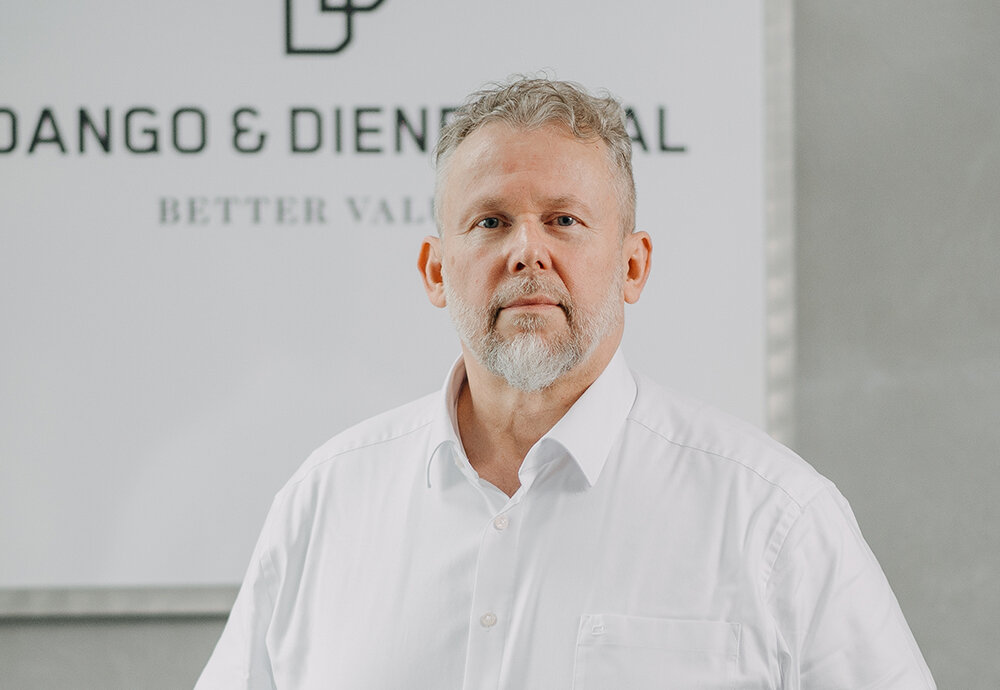
Herr
Volker Witzleb
Senior Sales Manager
T +49 271 401-4433
volker.witzleb@dango-dienenthal.de
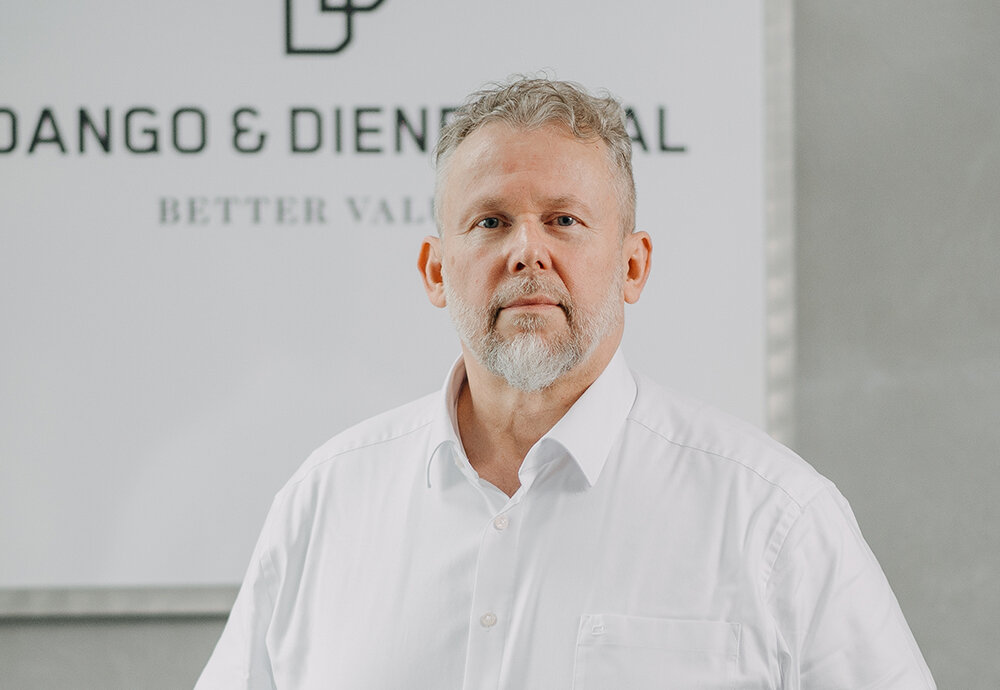
Herr
Volker Witzleb
Senior Sales Manager
T +49 271 401-4433
volker.witzleb@dango-dienenthal.de

Iysa Demir
Sales Manager Service
T +49 271 401-4332
iysa.demir@dango-dienenthal.de