SSM SERIES
Rail-bound forging manipulators
The rail-bound forging manipulators in our SSM series can position workpieces weighing between 10 and 3,500 kN in the press with the highest precision, ensuring an optimum forming effect with every stroke.
The performance of an open-die forging press depends not only on the stroke capacity of the press – equally important are the precision and dynamics of the manipulators.
HIGHLIGHTS
We have engineered our rail-bound manipulators for the forging of components in extremely demanding applications.
We look at all stages of the open-die forging process. Therefore, our manipulators are designed to deeply integrate with the data world of the forging shop in order to maximize the productivity of the complete press line.
The result: repeatable precision in forging and low total cost of ownership.
Our ERS system helps to save valuable resources while boosting the efficiency of the forging process.
THE BENEFITS AT A GLANCE
High efficiency along the complete production chain
- Quick, high-precision positioning
- Little reworking in subsequent process stages
- High accuracy of the angle of rotation
- Precisely contoured and reproducibly manufactured forgings
High process safety
- Deep digital integration
- Complete documentation of process data
High availability
- High long-term accuracy
- Low maintenance effort
MORE DETAILS
LONG-TIME ACCURACY GUARANTEED
Our SSM series manipulators run on rails. This and the electrically preloaded drives move the manipulators back and forth and bring them to a halt with the highest precision and accuracy of repeatability.
The unique single-mass concept of the D&D manipulators means that the moving drive and the actuating drive of the tongs are firmly connected. This enables a straightforward, sturdy machine design with very few moving parts and highest-precision control of the moving drive. The drive control is independent from the weight of the forged pieces.
The high long-term accuracy of the tong actuation guarantees that the forging is positioned in the press at exactly the right angle for each stroke.
IN THE PERFECT POSITION – QUICKLY AND PRECISELY
The highly dynamic axial piston motors of the optional ERS system reduce forging times. Because the motors use no throttle valves, there is no compression loss due to throttling. Therefore, the moving drive reaches its final speed earlier and will come to a halt faster.
When compared to the use of proportional valves, this results in up to 20 to 30 percent less time needed for the movements and overall shorter processing times for each forging. In addition the drives for moving the manipulator and those for actuating the tongs can perform various synchronistic overlapping motions. This means that the tongs can be brought in position while the manipulator is still moving, saving additional time with every stroke.
THE MOVING DRIVE
Positioning of the manipulator is performed by backlash-free pin-tooth gearing and therefore, based on the size of the machine, achieves an accuracy of +/- 1.5 to 5.0 mm in the direction of travel.
ACTUATION OF THE TONGS
Turning, opening and closing, lifting and lowering of the tongs are all hydraulically actuated. The vertical-horizontal compensation system “height reset” adjusts the position of the tongs automatically according to the press stroke. Turning the tongs as precisely as possible is crucial for the performance of the entire process. Here our patented valve wear compensation system ensures utmost precision at all times. The long-time stability is extraordinarily high: even after several years of operation the system works just as precisely as on the very first day.
Thanks to our high-precision, permanently stable control system the rotation of the tongs is adjusted exactly to the press stroke.
You have the choice
To best meet the characteristics of the forgings, we manufacture the tongs either using cast components or a welded construction of forged components. This flexibility enables us to comply with the most specific customer requirements.
We optimize each individual manipulator tong according to the flow of force.
EFFECTIVE COMMUNICATION
A high-end forging manipulator never operates as an isolated unit. Integrating the machine into the complete process is a basic requirement for maximum productivity. This includes linking with higher-level systems, communication with other process stages and gapless documentation. Our manipulators are compatible with the process control systems of all forging press manufacturers.
The sensors in our manipulators provide comprehensive data and measured values based on which our customers can trace back each individual stroke and prove to their customers at any given time that the supplied forgings comply exactly with the specifications in the order.
The acquired data is used to optimize the process.
STRAIGHTFORWARD DESIGN
DANGO & DIENENTHAL is the only manufacturer of forging manipulators to design the machines with a single central control block for all key hydraulic functions. The hydraulic lines are easily accessible. If necessary the lines can be exchanged quickly and conveniently. When our engineers design a machine, ease of accessibility of all components is a requirement of high priority.
We often hear our customers’ maintenance staff say that they are impressed with the maintenance friendliness of our manipulators. All components are easily accessible thanks to the spacious interior of the machines. That also applies to the pin-tooth gearing which is located on the exterior of the machine for very convenient access.
Furthermore, the axial piston motors that drive our machines require much less frequent maintenance than systems using proportional valves.
The benefits: lower maintenance effort and higher availability.
SAFETY FIRST
The manipulators come with a safety rope to protect the area next to the machines, while a protective fence protects the area between the press and the manipulator. Where this is not possible, the manipulators can be fitted with optional laser scanners to observe the area behind. The moving gear will automatically stop when the scanners detect an object.
We also support our customers with the installation and commissioning of our machines. If a conformity declaration is required – in the case of a major conversion for example – we will provide our customer all information and documents needed for the CE certification.
Careful use of resources
The latest generation of our SSM series sets new standards: The Energy Recovery System (ERS) helps save up to 70 % of the energy previously required for driving the machine.
Moreover, our highly dynamic axial piston motors reduce the time needed for positioning, thus boosting the performance of the press. That results in a 30 % reduction in overall energy consumed by the machine.
The ERS system recovers much of the energy used for acceleration, which keeps the energy consumption of our manipulators very low.
THE RIGHT ORIENTATION
Turntables significantly reduce handling times in open-die forging operations: for example, when transporting the forging from the furnace to the manipulator or when rotating the forging by 180°.
Having turntables in place also means that the forging process does not depend on the availability of the cranes in the press shop. This ensures that forging schedules can be reliably maintained.
We supply three types of turntables:
- Mobile: This turntable moves into the driveway of the manipulator, turns the forging and immediately moves back out again.
- Retractable: Our pop-up turntable is installed flush with the floor. It rises when it is needed and retracts when the job is done.
- Swiveling: In this case, the table is permanently placed next to the press. When needed, it is temporarily swiveled into the driveway of the manipulator and then swiveled back again.
Technical data
Carrying capacity
kN
Load moment
kNm
Block tongs gripping range
mm
Disk tongs gripping range
mm
Upper stroke position of tongs
mm
Drive power
kW
Contacts
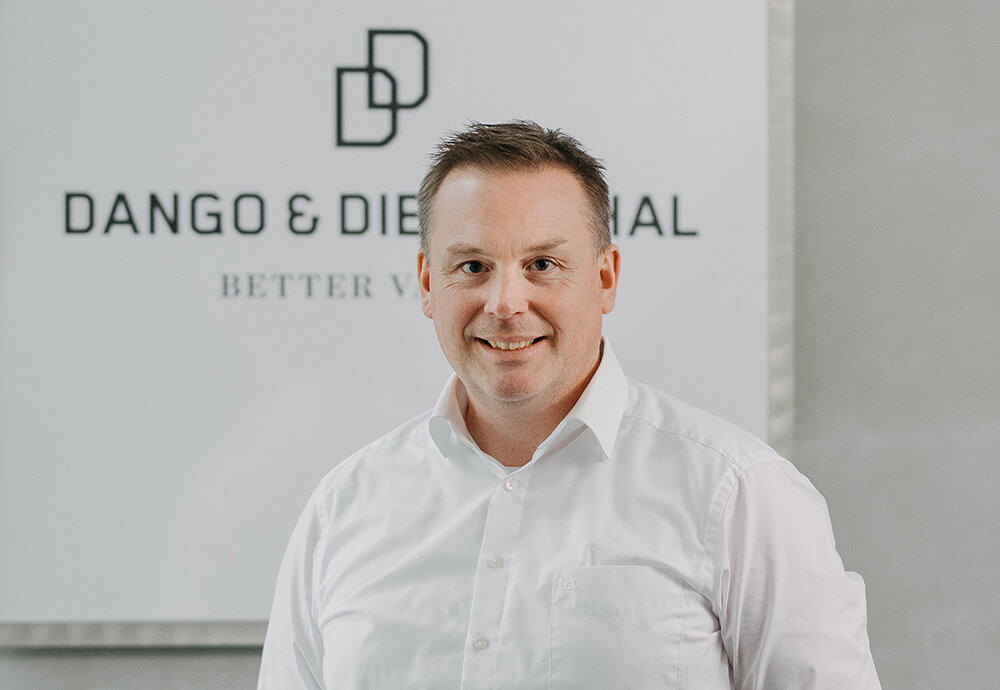
Herr
Andree Nöh
Senior Sales Manager
T +49 271 401-4491
andree.noeh@dango-dienenthal.de
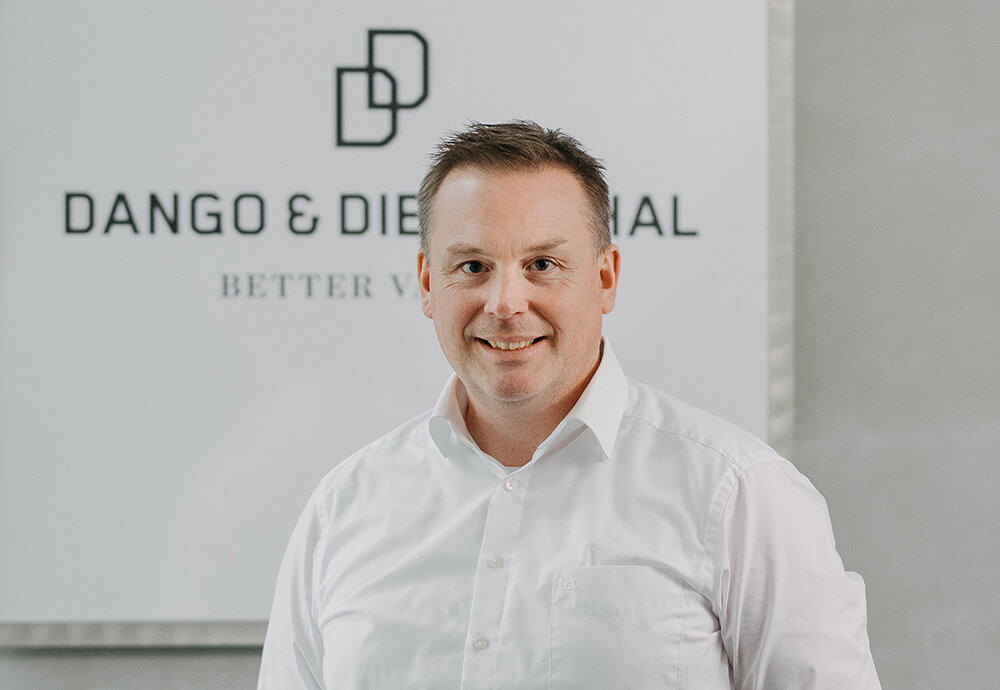
Herr
Andree Nöh
Senior Sales Manager
T +49 271 401-4491
andree.noeh@dango-dienenthal.de
T
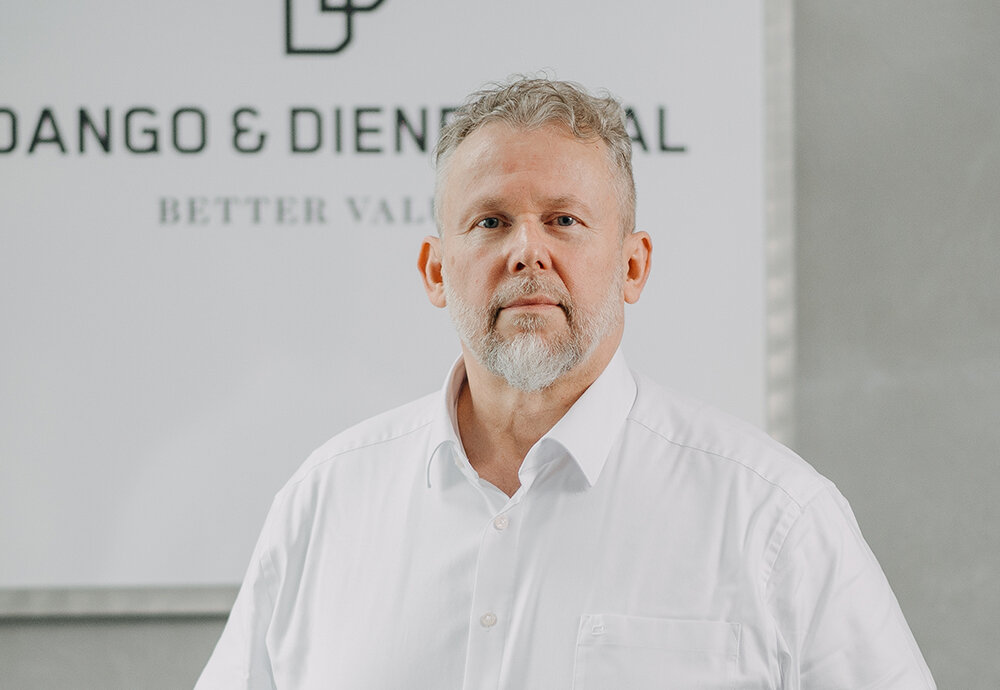
Herr
Volker Witzleb
Senior Sales Manager
T +49 271 401-4433
volker.witzleb@dango-dienenthal.de
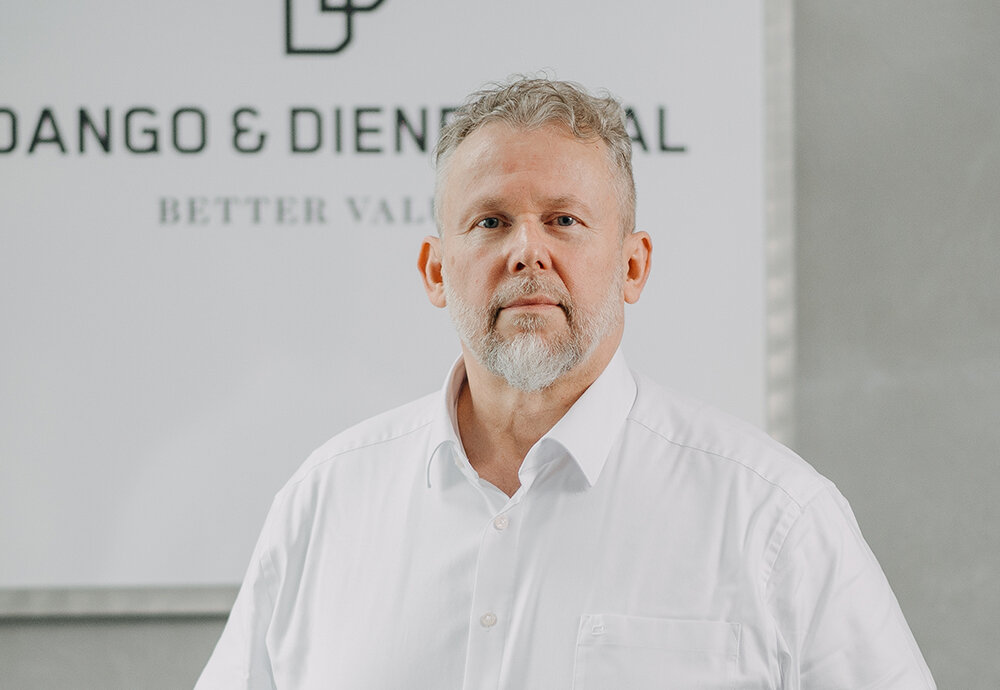
Herr
Volker Witzleb
Senior Sales Manager
T +49 271 401-4433
volker.witzleb@dango-dienenthal.de

Iysa Demir
Sales Manager Service
T +49 271 401-4332
iysa.demir@dango-dienenthal.de